Wet Electrostatic Precipitator Wesp Manufacturers In India
.png)
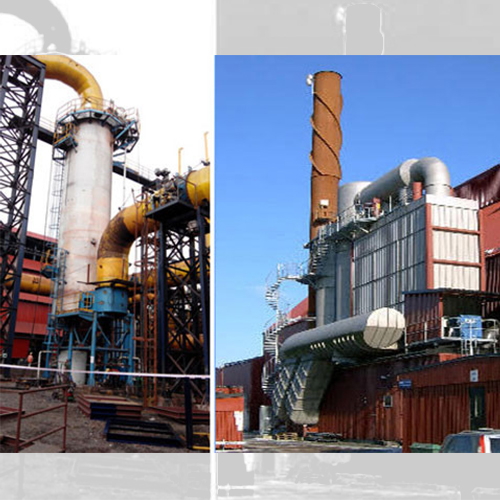
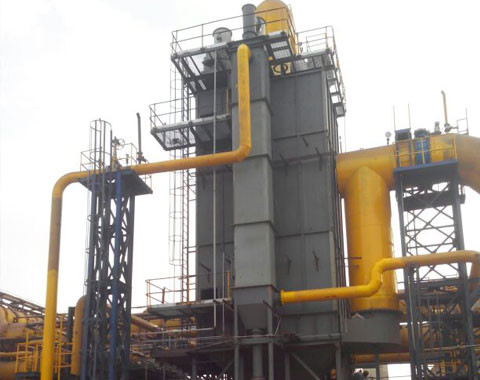
A Wet Electrostatic Precipitator (Wet ESP) is an air pollution control device that is designed to remove fine particulate matter and aerosols, as well as certain gases, from industrial exhaust gases. It accomplishes this through the application of electrostatic forces, as well as the use of water or other liquid to enhance the capture of particles. Wet ESPs are commonly used in various industrial applications where the removal of fine particulates, submicron-sized particles, and soluble gases is necessary.
Here is a description of the key components and operation of a Wet ESP:
Components of a Wet Electrostatic Precipitator:
- Inlet Section:The polluted gas stream, which may contain fine particulates and aerosols, enters the Wet ESP through an inlet duct.
- Gas Distribution Plate: This component is located at the inlet of the Wet ESP and helps evenly distribute the gas flow to ensure efficient particle charging and collection.
- Electrostatic Precipitator Section: This section includes a series of high-voltage discharge electrodes (negative) and collecting electrodes (positive). These electrodes are spaced apart and aligned in a way that creates a corona discharge and a strong electric field.
- Washing System: A continuous flow of water or other liquid is introduced into the Wet ESP. The liquid is sprayed or cascaded over the collecting electrodes, forming a thin film or mist. The liquid is used to provide conductivity and improve the collection efficiency by enhancing the capture of charged particles.
- Collection ElectrodesThe positively charged collecting electrodes are designed to attract and capture the negatively charged particles and droplets from the gas stream
- Outlet Section: The cleaned gas exits the Wet ESP through an outlet duct.
Operation of a Wet Electrostatic Precipitator:
- Ionization and Charging: When the polluted gas passes through the electrostatic precipitator section, the gas molecules are ionized by the corona discharge created by the high-voltage discharge electrodes. This results in the charging of fine particles and aerosols present in the gas stream.
- Particle Collection: The charged particles are attracted to and collected on the grounded collecting electrodes. The liquid film or mist on the collecting electrodes aids in the capture of the charged particles. This process is highly efficient for submicron-sized particles and fine particulates.
- Droplet Collection: Any soluble gases or aerosols in the gas stream are also captured by the liquid film and are removed from the gas stream as droplets.
- Cleaning and Maintenance: Periodically, the collected particles and droplets are washed away from the collecting electrodes and collected for disposal.
Benefits of Wet Electrostatic Precipitators:
- Highly Efficient: Wet ESPs are capable of capturing submicron-sized particles and fine particulates, making them suitable for applications requiring high particle removal efficiency.
- Effective Gas and Vapor Control: Wet ESPs can capture and remove soluble gases, aerosols, and volatile organic compounds (VOCs).
- Reduced Re-entrainment: The use of liquid in the process minimizes the re-entrainment of particles into the gas stream.
- Suitable for High Temperature and High Humidity: Wet ESPs are effective in applications with high-temperature and high-humidity exhaust gases.
- Compliance with Emission Standards: They help industries meet environmental regulations and emission standards.
Wet ESPs are commonly used in industries such as cement manufacturing, pulp and paper production, waste incineration, and various chemical processes where the control of fine particulates and gases is critical for environmental compliance and air quality improvement.
Industrial applications of WET ESP
Wet Electrostatic Precipitators (Wet ESPs) are employed in various industrial applications where the control of fine particulate matter, aerosols, and certain gases is essential to ensure compliance with environmental regulations and maintain a clean and safe working environment. Here are some common industrial applications of Wet ESPs:
- Waste Incineration:
- Municipal Waste Incinerators: Wet ESPs are used to control emissions of fine particulates and acid gases generated during the incineration of municipal solid waste.
- Pulp and Paper Industry:
- Recovery Boiler Emissions: Wet ESPs help control emissions from recovery boilers, reducing particulates, sulfur compounds, and other pollutants in the production of pulp and paper.
- Metal Processing:
- Non-Ferrous Metal Smelting: Wet ESPs are used in the non-ferrous metal industry to capture and control emissions of fine particulates and heavy metals produced during smelting processes like aluminum and zinc production.
- Chemical Manufacturing:
- Chemical Process Emissions: Wet ESPs are applied to control emissions of corrosive gases, volatile organic compounds (VOCs), and hazardous chemicals generated in various chemical manufacturing processes.
- Mineral Processing:
- Mining and Ore Processing: Wet ESPs are used to control emissions of dust, metals, and sulfur compounds produced during mining and ore processing operations.
- Power Generation:
- Biomass and Biomass Co-firing: Wet ESPs help reduce particulate emissions in power plants using biomass and co-firing biomass with coal.
- Woodworking Industry:
- Wood Dust Control: Wet ESPs are employed to control emissions of wood dust generated in woodworking and furniture manufacturing operations.
- Refineries:
- Petroleum Refineries: Wet ESPs are used to control emissions of particulates and sulfur compounds, contributing to improved air quality in the refining industry.
- Cement Manufacturing:
- Kiln Exhaust Gas Treatment: Wet ESPs are used to capture particulates, as well as alkali and sulfur compounds generated during the cement production process.
- Municipal Water and Wastewater Treatment:
- Odor Control: Wet ESPs help control odorous emissions in sewage treatment plants and wastewater facilities.
- Textile Industry:
- Dyeing and Finishing Operations: Wet ESPs are employed to control emissions of VOCs and chemical fumes from textile dyeing and finishing processes.
- Electronics Manufacturing:
- Semiconductor Manufacturing: Wet ESPs are used in cleanroom environments to control emissions of hazardous gases generated during semiconductor manufacturing.
- Glass Manufacturing:
- Glass Melting and Forming: Wet ESPs help reduce particulate emissions and control emissions of various pollutants in the glass manufacturing industry.
- Food Processing:
- Odor Control: Wet ESPs are used in facilities like rendering plants and meat processing facilities to control odorous emissions.
Wet ESPs are chosen for these applications based on their ability to efficiently remove submicron-sized particles, fine particulates, and certain gases, including acid gases and volatile organic compounds. They play a critical role in reducing emissions, protecting the environment, and ensuring regulatory compliance in various industrial processes.